Formula 1 has long made intensive and extensive use of 3D printing. In wind tunnel testing models, structural components on cars, mirrors and other components and in the chassis and body of the car itself. Special material grades of reinforced plastics and matrix materials have been developed specifically for Formula 1 and other motorsports. Lately we’ve seen F1 teams and 3D printing companies embrace each other very publicly.
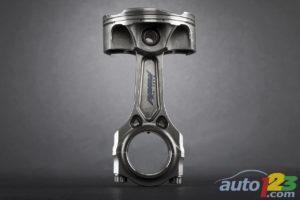
A conventional F1 rod and piston made over 17 years ago.
F1’s love affair with 3D printing has been going on much longer than this, however. Only, this being F1, they’ve always been secretive about it. 3D printing lets you make shapes that you can not make with another technology. You can save weight by designing forms that would not work either using other means. Our technology is ideally suited for one-offs or low-volume products and this is exactly what F1 cars are. In creating new geometries and new shapes to push the envelope on weight and speed 3D printing is an ideal technology to do this. F1 teams have for years used 3D printing in many different applications.
A new story details a move by Magneti Marelli and Ferrari to publicly talk about using 3D printing metal inside an F1 car. A steel alloy will be used in a honeycomb structure to construct a novel piston design that gives high strength and low weight. The piston is part of the micro-injector design for the new Turbulent Jet Ignition System. This new Magneti Marelli design will increase the pressures in the engine significantly requiring the updated 3D printed part.
The choice for a steel part is rather interesting for this type of application. Titanium and aluminum parts would also be options as would high-temperature alloys such as hastelloy. Materials such as EOS’ CobaltChrome MP1 which is a cobalt-chrome-molybdenum-superalloy would for example have very good high temp applications and is used in aerospace. EOS MaragingSteel MS1 could also be an alternative. EOS NickelAlloy IN625 would be a great high temperature material and both it andEOS Titanium Ti64 are suggested materials for motorsports. On Arcam systems their Titanium and Inconel would also be interesting candidates. It is puzzling why the team would choose a steel alloy for this application.
Interestingly since EOS has partnered with Williams F1, would GE be the logical partner for Ferrari? GE has sponsored F1 before but did so for teams that were not exactly close to winning. Airbus has also sponsored F1 and has quite a bit of metal 3D printing capacity. Wouldn’t it be fun if metal 3D printing became a very public F1 battle?
We hope that the veil will be lifted on 3D printing’s extensive use in F1 and will keep you updated for more! Discuss in the Ferrari forum at 3DPB.com.