The goal of a recent case study was to illustrate the design and construction of the driver on behalf of Krone, a world leader in custom engineered golf equipment. Composite materials and titanium have been used in the golf industry for a long time, but no one has taken full advantage of how the materials are used to increase design and performance. Krone needed to break away from traditional mass produced manufacturing techniques, and instead use cutting-edge materials and processes, as well as work with industry manufacturing leaders to develop a driver that will set a new standard, both in how it performs on the course, and in the quality of the final product.
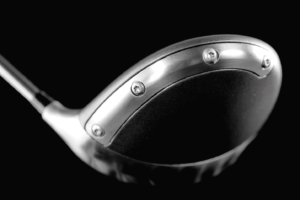
“We see the opportunity to do something revolutionary in the golf industry and design a superior product through the use of intelligent design, innovative materials, and high tech manufacturing methods,” says Marc Kronenberg, Krone Golf CEO.
The company has certainly done its research, testing multiple manufacturing processes like Direct Metal Laser Sintering of titanium and 3D printing “wax” or master patterns for casting. While some early results showed promise, there were also problems with accuracy, repeatability, and part quality. So they decided to partner with the CRP Group for the project. Two CRP Group divisions were put on the project team as technical partners for very specific purposes: The 3D printing department of CRP Technology created the prototypes and end parts, using additive manufacturing and high-precision CNC machining. CRP Meccanica coordinated all aspects of the project among Krone, CRP Technology, and the design consultants.
Past technologies in creating golf clubs were fairly labor intensive and expensive, so they’re not great for small runs or customized parts. The casting and forging processes often require secondary operations, due to wide tolerances and part-to-part variations. Titanium used in the post-welding process cannot be cast or stamped any thinner than the industry norm: welding creates a heat-effected zone, so it can cause deformation in thin areas. That’s why CNC machining is so helpful: you can better control thickness, and additive manufacturing lets you create very stiff, lightweight structures and 3D lattice geometries that were unheard of before.
The 3D printing and CNC machining blend lends speed to the parts manufacturing process: the additive manufacturing technology takes much less time than designing and producing a tool for injection molding, and 3D printing gives engineers more flexibility to make design improvements.
“We plan to continue to work closely with CRP to refine the design so that it can take full advantage of their CNC and Additive Manufacturing processes and bring the concept of ‘mass customization’ for individually made golf components to market by the end of this year,” says Kronenberg. “The fit between the CNC machined parts and the Windform is exactly as designed. I can say from the design point of view that the use of Windform SP and titanium has allowed me to really push the limits for the ‘performance’ of the golf club: its performance level, as predicted in computer simulations, is unlike any other golf club available today.”
Krone golf clubs are guaranteed for life, and they are refurbished and tuned each year. For more details about the golf club, you can read more in the case study here and take a look at the video below to see how the 3D printed KD-1 is created:
Discuss in the KD-1 forum at 3DPB.com.
[Images courtesy Krone, provided to 3DPrint.com by CRP Group]