The city of Delft in Holland is famous for its blue and white pottery, for its native son, the Dutch Baroque painter, Johannes Vermeer, and for its picturesque historic town center, complete with canals. As with the majority of his colleagues in other cities in the Low Countries, Vermeer’s paintings emphasized realism, accomplished by painstaking observation and a perfectionist’s technical skill. Vermeer’s paintings almost always feature human figures, who are central to a given image. However, like his fellow painters, he was compelled to describe the interiors of 17th-century Dutch homes, particularly those of the comfortable, well-to-do merchant class who were happy to display their wealth during this period known as “the Golden Age” in the Netherlands. Of the thousands of still-life paintings of the era, many featured food and the vessels in which it was served. Such imagery was demonstrative of the refined painting skills of the artist but also the acquisitions that great wealth afforded many a Dutch burgher.
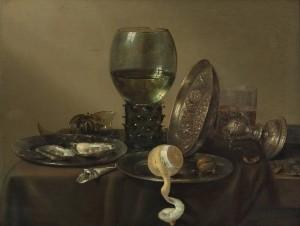
Still-Life with Oysters, a Rummer, a Lemon and a Silver Bowl, 1634
Willem Claesz. Heda. Museum Boijmans Van Beuningen in Rotterdam, NL.
This still-life from 1634 by the Haarlem painter, Willem Claesz. Heda is one such image–a picture of Dutch material wealth and luxury. The glass–and glassware in general–is almost ubiquitous in 17th-Century Netherlandish still-life paintings but was also omnipresent in the homes of the well-to-do. It was likely produced in the Netherlands or Germany. The Museum Boijmans Van Beuningen in Rotterdam, not far from Delft, has a variety of this usually green- or amber-tinted glass in its collection, including glassware made in Delft. The cups are less elaborate than the stemware seen in the Heda painting, but it is revered nonetheless as exemplary of Netherlandish artisanal mastery.
Recently, a team of technicians and artists led by Dutch artist, Maaike Roozenburg, collaborated on a project to produce 3D-printed replicas of 17th-century Delft glassware from the Museum Boijmans van Beuningen to, explains one team member, “enable people to use objects they would normally only see behind the glass in a museum.” The glasses, some of which were understandably in less-than-perfect condition, were scanned using a “medical CT scanner.” “This gave us,” reports that same team member, “over 1000 sections of the glass in a DICOM format.”
The process the team used, in some ways as painstaking as that of the Golden Age painters, was documented with videos and detailed descriptions of each step. As they worked, the team experimented with different materials and methods in the interest of refining its process and achieving specific results, porcelain versions of the glasses that reflected their current, imperfect state but were nonetheless sturdy and functional.
They encountered problems in converting the 3D models they achieved via scanning into workable, positive prints. One major problem, reported one team member, was that the scanner interpreted cracks and shallow holes in the original glassware as deep holes and, as a result, produced imperfect, permeable 3D prints. However, the expertise of Roozenburg proved invaluable as solutions were discovered and the project moved forward.
Both low- and high-resolution prints were made of the cups using three different kinds of 3D printers and different materials to determine which one worked best. From the best results, negative molds were made from plaster and wood, and then printed using a plaster printer. In this phase of the project, Roozenburg’s skills as an experienced artisan were invaluable. Determining which plastic was most compatible in this step included finding a material with which to coat the mold to prevent sticking in the casting process. The complicated design patterns on the exteriors of the glass cups made this mold casting problematic but certainly surmountable. In the end, the team decided that candle grease was the solution, and they were able to proceed with the next steps. When a satisfactory negative mold was produced, the final product, a porcelain replica of each original glass cup, was produced on a 3D porcelain printer. The end results are true works of art in their own right, beautiful porcelain cups that retain references to the imperfections of the original glasses.
Let’s hear your thoughts on this creative application of 3D scanning and printing in the 3D printed Dutch glasswear forum thread on 3DPB.com